ENB사의 파티클보드 생산 공장은 후지산 산기슭에 위치한 광대한 공업단지(신산업 집단지역 공업단지)에 위치한다<사진 1, 2>. 부지면적은 도쿄 돔 2개분에 상당하는 약 9만3,000㎡이다. 규모가 큰 간토(関東)시장을 시야에 넣으면서 서일본의 수요를 겨냥하여 장소를 선정했다. 무엇보다도 국도 246호선으로부터의 접근이 좋고 또 도메이(東名) 고속도로의 인터체인지에서도 가깝다.
2023년도에는 공업단지로부터 그렇게 멀지 않은 장소에, 신토우메이(新東名)고속도로의 스마트 인터체인지가 새롭게 개통됨으로써 물류면에서 한층 더 우위성이 더할 것으로 기대하고 있다.
ENB사로부터 남쪽에 위치한 스소노시(裾野市)에서는 가까운 미래를 응시한 도시 ‘Woven City(우븐 시티)’의 건설이 진행되고 있다. 장래 2,000명이 산다고 하는 이 거대한 프로젝트로 파생되는 수요도 매우 매력적이라고 할 수 있다.
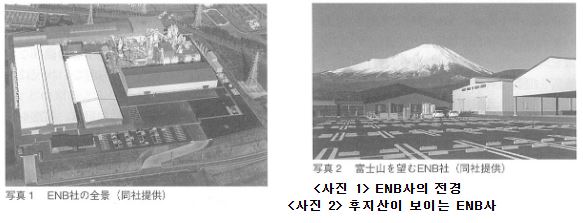
2.2 생산능력, 월간 1만5,000톤
다음으로 ENB사의 주요 설비를 살펴보면, 심장부에는 독일의 Siempelkamp사제의 연속 프레스를 도입했다<사진 3>. 국내 최장의 47m의 길이를 자랑한다. 생산능력은 1만5,000톤/월으로 1개 라인의 생산공장에서는 국내 최대이다.
당사의 경우, 파티클보드의 생산에 연속 프레스를 도입하는 것은 이번이 첫 케이스가 된다. 연속 프레스에 대해서는 일본제지주식회사와의 합작사업(1995년) 시에 MDF제조의 N&E주식회사에 도입했기 때문에 일정한 지견(知見)을 가지고 있었다. 그렇지만 그 때 제조업체는 같은 독일에서도 Dieffenbacher사였다.
한편, 노보판사에서는 파티클보드를 생산하는 2개 공장 모두 연속 프레스를 도입했고 그 중 1개 공장에서 Siempelkamp사제를 이용하고 있다. 버전은 약간 오래되지만 동사가 이미 설비와 시스템의 노하우를 축적한 것은 ENB사의 공장 시작에 크게 기여했다.
덧붙여서 ENB사에서는 기본적으로 최초의 칩파쇄에서 Cooling Turner에 의한 조습까지 Siempelkamp사 또는 그 산하기업의 설비를 이용하고 있다. 이와 같이 진행한 것은 유지보수의 부담경감과 생산의 효율화가 목적이다. 물론, 이 공정에서 동사 이외 복수의 기계업체의 설비를 설치하는 검토도 없지는 않다. 하지만, 일반적으로 불편이 생기기 쉽다는 사례도 있으므로 리스크를 피하는 의미에서도 동일 제조업체의 설비로 구성했다.
덧붙여 실제로 제품이 완성된 후의 마무리 공정은 별도이고 표면 마무리의 Sander나 소할용(小割用)의 절단은 실적이 있는 국내 제조업체의 설비를 채용했다.
그 밖에 주요 설비로는 중유(重油)를 이용하지 않는 바이오매스 보일러를 도입했다<사진 4>. 보일러의 역할은 2개가 있다. 하나는 목재 칩을 건조시키기 위한 증기를 만드는 것, 또 다른 하나는 연속 프레스로 매트를 열압 압축하기 위한 열원을 만드는 것이다.
반입한 목재 칩 가운데 파티클보드에 적합하지 않는 것 만을 선별하여 보일러의 연료로 하고 있다(Thermal 리사이클). 화석연료를 사용하지 않는 바이오매스 보일러는 틀림없이 온실효과가스의 배출억제에 공헌하고 있다. 다만, 어디까지나 파티클보드 제조업체의 기본자세는 ‘Material 리사이클>Thermal 리사이클’이다. 이러한 점에서 최초부터 목재 칩을 연료로 사용하는 바이오매스 발전소와는 구별을 분명히 하고 있음을 여기서 강조해 두고자 한다.
2.3 단계적으로 생산량의 증가 실시
ENB사에서는 2022년 5월에 First Board의 생산을 행하여 11월에 JIS(일본산업규격)인증을 취득한 후 실질적인 상용 생산을 단행했다<사진 5>. 동절기에 원재료로 목재 칩을 확보할 수 있었기 때문에 2023년 2월 시점에서의 생산량은 약 5,000톤/월에 도달했다. 앞으로 단계적으로 끌어올려 2023년도 말을 목표로 완전생산까지 접근해 나갈 계획이다.
되돌아보면, 2019년의 회사설립에서 약 3년 지났지만 그 과정은 반드시 순탄하지는 않았다. 당초 계획에서는 180억엔을 투자해 2021년 4월부터의 상용 생산을 전망하고 있었다. 하지만, 도중에 계획 재검토를 도모할 필요가 있었고 또 신형 코로나 바이러스의 영향으로 독일로부터의 Supervisor(전임기술자, 사진 6)의 일본방문이 막히는 등 생산 개시의 스케쥴은 1년반이나 늦어지는 결과가 되었다. 이 사이 제반 자재와 인건비, 물류비 등의 상승도 있어 총투자액은 최종적으로 70억엔이 증가하여 250억엔이 되었다. 만약 합작이라는 형태가 아니라 1개사 단독으로 프로젝트를 진행했다면 이러한 거액의 투자는 어려움이 극에 달했을 것이다.
2.4 ‘Green Loan’으로 자금 조달
앞에 언급한 바와 같이 총투자액은 250억엔이며 이 가운데 30억엔은 토지취득 비용이고 나머지 220억엔(공장건설 자금) 가운데 당사가 보증하는 143억엔(65%)에 대해서는 ‘Green Loan’으로 조달했다.
‘Green Loan’이란, 기업이나 자치체가 환경개선 효과가 있는 사업(그린 프로젝트)에 한정하여 이용 가능한 융자를 말한다.
당사 그룹에서는 2023년도를 최종 연도로 하는 중기경영계획 중에 ‘목질보드사업의 강화와 확대’ 및 ‘SDGs의 대처’를 내걸고 있다.
2.2항에 바이오매스 보일러와 연계하여 온실효과가스의 배출억제에 대해 언급했지만 ENB사에 있어서 목질보드의 생산에 따른 미이용재의 유효 활용이나 목재자원의 순환이용, 게다가 남양재로부터 파티클보드로의 원재료 전환은 장기적으로 보아 SDGs의 목표달성에 기여하는 시책에 합치한다<표 2>.
당사 종래의 다단식과 비해 ENB사의 연속식(連續式)에서는 연간 어느 정도의 온실효과가스 삭감(환경개선효과)을 전망할 수 있을까 하면, 상세한 계산식은 생략하지만 생산공정에 있어서의 Loss가 감소하여 대충 연간 7, 600CO2톤이 될 전망이다.
게다가 2021년 10월에 임야청으로부터 ‘건축물에 이용한 목재와 관련된 탄소 저장량의 표시에 관한 가이드 라인’이 공표되어 파티클보드의 탄소 함유율을 0.451로 하는 것으로 제시되었다. 앞으로는 이 수치를 활용하여 파티클보드의 탄소저장 효과를 넓게 주지(周知)시키는 것도 필요하게 될 것이다.
2.5 벽(壁)을 넘어 앞으로 ‘Floor 대판(台板)’으로 이용
ENB사에서는 구조용 외, 화장용, 맨션바닥용, 목공용, 복합 Flooring용 기자재(Floor 대판) 등을 생산한다. 제품은 출자비율(표 1 참조)대로 당사가 65%, 노보판사가 35%를 맡아 각각 판매한다.
이 구조용 파티클보드는 상담이 결정되었기 때문에 출하가 시작되어 벌써 현장에서 시공이 시작되었다<사진 7>.
구조용 합판과 마찬가지로 목질보드의 OSB, 또 비목질(非木質)보드에 이르기까지 경합하는 제품은 적지 않지만 구조용 파티클보드는 지금 완전하게 시장에서 인지되어 있어 거주지의 안전에 대한 요구를 배경으로 앞으로도 신축과 리노베이션을 불문하고 계속적인 수요를 전망할 수 있을 것으로 보고 있다.
덧붙여서 ENB사의 구조용 파티클보드의 제품명은 회사명과 같은 ‘EN BOARD’로 하는 것이 당사와 노보판사, ENB사와의 사이에서 결정되었다.
그런데 구조용 이외의 제품의 가운데 특히 Floor대판의 생산은 당사에 있어서 오랜 세월의 꿈이었다. 과거에 몇 번이나 도전했고 2007년에 제2차 우드 쇼크가 일어났을 때는 ESP(Eidai Sustainable Panel)로 불리는 시작품도 있었다. 하지만 결국, 과거의 시작품은 모두 합판과 비해 무겁고 또 마루 난방에서의 열변화에 견딜 수 없다고 하여 실용화에는 이르지 않았다. 이는 구형의 설비(다단 프레스 방식)에서는 아무래도 넘을 수 없는 ‘벽(壁)’이었다.
이러한 역사도 있어 당사에서는 ENB사에서 생산하는 Floor대판에 많은 기대를 걸고 있다. 당사에서는 현재, ENB사의 Floor대판을 이용한 복합 플로어링의 개발을 추진하여 실용화에 임하고 있다.
앞으로는 Flooring 뿐만이 아니라 취급하고 있는 제품에 대해 가능한 것부터 파티클보드로 전환을 도모하여 장래적으로는 타사에 대해서도 제안을 해 나갈 방침이다.
3. 앞으로의 파티클보드 산업 전망
3.1 약 30년 전에는 15개사 16개 공장 가동
약 30년전, 1991년 시점에서 국내에는 파티클보드공장이 15개사 16개 공장이 가동하고 있었다. 2023년 2월 시점에서의 국내 파티클보드 공장은 5개사 4개 공장으로 감소되어 10개사 12개 공장이 되었다(당사 조사, ENB사 포함).
그 동안 파티클보드, 섬유판, 합판의 국내 공급량이 크게 변화되었다<표 3>. 또한, 신설주택착공 호수도 크게 감소했다<표 4>.
<표 3>에서 알 수 있듯이 가장 공급량이 감소한 것은 국산 합판이다. 1991년 당시는 아직 남양재 원목을 수입하여 박판, 중후판, 콘크리트 거푸집용을 생산하는 합판제조업체가 국내에 다수 존재하고 있었다. 이것이 일제히 철폐와 폐업되었고 상대적으로 목질보드의 점유율이 증가하는 결과가 되었다. 다만, 양적으로 증가한 것은 국산이 아니라 수입제품의 파티클보드와 섬유판이다.
가까운 장래에 ENB사가 완전 생산으로 이행하여 월간 1만5,000톤의 파티클보드를 상시 공급할 수 있게 될 경우 재적 베이스로는 연간 250천㎥(밀도: 0.72톤/㎥ 환산)가 추가된다.
만약, 2021년 시점부터 그다지 큰 변화가 없다면, 단순 계산으로 국산 파티클보드의 공급은 1,254천㎥로 2021년대비 약 25% 증가하여 파티클보드 점유율(국산, 수입 합계)은 20%에 달하게 된다.
3.2 심화되고 있는 원재료 쟁탈전
마지막으로 파티클보드 업계를 둘러싼 정세에 대해 고찰하고자 한다. 앞에 언급한 바와 같이 파티클보드 그 자체의 미래는 밝다. 하지만, 생산하는 제조업체 모두가 똑같이 밝다고 하는 것은 아니다. 아마 공장의 신규 건설은 지금 이상으로 어려워질 것이다. 그 이유는 ①거액의 설비투자(갱신 포함) ②주택수요의 축소 ③안정적인 원재료(목재 칩) 확보에 어려움 증가 등 이상의 3점으로 집약된다.
①에 대해서 보면, 1991년의 시점에서 차세대의 생산방식이라는 연속 프레스를 도입하고 있던 제조업체는 1개사(신설) 뿐이었다. 오늘날에는 조업하고 있는 10개사 12개 공장 가운데 절반인 5개사 6개 공장이 연속 프레스를 도입하고 있다(당사 조사). 구형의 생산설비를 보유한 각 제조업체는 장래 어떻게 할 것인지? 머지않아 선택을 강요당하게 될 것이다.
②에 대해서는 더 설명할 것도 없지만 제조업체에 있어서는 비주택 분야 등 새로운 수요의 창출이 필요하다.
③에 대해서는 파티클보드 업계가 앞으로도 한층 엄격해질 것으로 보인다. 전국에 건설된 바이오매스 발전소와의 사이에서 원재료인 목재 칩의 쟁탈전이 한층 더 격렬해질 가능성이 매우 높기 때문이다.
2021년 목질바이오매스 발전소는 283개소로 추계(推計)되어 지금부터 불과 2년 후의 2025년에는 523개소, 2030년에는 626개소까지 증가할 것으로 전망하고 있다.
물론, 이러한 바이오매스 발전소 중에는 원재료가 목질계가 아닌 메탄 발효가스계(하수오니, 식품 폐기물 등)로 직접 경합하지 않는 곳도 있다.
하지만, 현재 일본은 만성적인 에너지 부족의 상황에 있어 에너지 자급율을 높이기 위해 Thermal 리사이클 전제(前提)의 시설이 한층 더 증가하게 되면 파티클보드 제조업체에 있어 압력이 되는 것은 필연의 정세이다.
4. 결언
ENB사는 현시점에서 국내 최대 파티클보드공장이며 게다가 품질에서도 국내 최고 수준의 제품을 생산할 수 있는 제조업체이다. 하지만 앞에 언급한 바와 같이 앞으로의 정세는 결코 낙관할 수 없다. 그러므로 자만하지 않고 오히려 시종 위기감을 갖고 파티클보드의 생산을 행하게 될 것이다.
이와 같이 당사에서도 위기감을 가지고 새로운 용도 개척이나 신제품의 개발을 추진해 나갈 방침이다. 이렇게 하면 목질보드사업에 대해 새로운 길이 열릴 것으로 확신하고 있다.